A
Study in ESD
Floor Coating Conductivity
ESD Floor Finish, ESD
Concrete Sealer, ESD Epoxy
Overview and goals: The purpose of
the following testing is to identify floor coatings that fully comply with the
latest recommendations of ANSI ESD S 2020-2014 page 4 tables 2, TR-53
Compliance Verification. TR-53 requires readings taken using portions of
ANSI/ESD STM7.1. This test method requires a compliant megohmmeter capable
of achieving an output of 10 to 100 VDC and measuring electrical resistance
in the range 1.0E02 to 1.0E14. The output of said device is coupled with
specialty electrodes of a specific size and density. Although not a
requirement of TR-53, good practice dictates taking Pont to Point (PTP) resistance
calculations using two electrodes. In this testing an electrical charge of
either 10 or 100 volts is generated and sent to an electrode. The charge
(voltage) travels through and across the flooring and the electrical
resistance value is measured to another electrode positioned 36” from the
first electrode. The test instrument measures the resistivity/conductivity
and presents it in Ohms.
Resistance to Ground (RTG) testing IS a requirement of TR-53. It is
accomplished using the same instruments. However, only one electrode is placed
on the substrate while said megohmmeter is grounded to an approved
electrical ground. In this scenario an electrical charge of 10 (for static
conductive flooring) or 100 volts (for static dissipative flooring) is
generated and sent through the electrode and the flooring substrate. The
resistance of said electrical charge is measured to the reliable ground
point in the facility and presented in Ohms.
TR-53 also requires readings taken using portions of ANSI/ESD STM97.1. This
testing is accomplished using the aforementioned test instrument. However, in
this test the megohmmeter is set to generate a 100 volt charge. One of
the two leads from the instrument is grounded. The second lead is terminated
to a hand held electrode. Said charge is generated and sent through a
technician standing on the ESD flooring while wearing standard industry
compliant heel grounders or ESD Footwear. The package resistance of the
technician, their footwear and the flooring is measured on the instrument
with readings presented in Ohms.
To pass ANSI/ESD S20.20-2014 (page 4, table
2) TR-53 Flooring Compliance Verification the electrical resistance of all
aforementioned testing must be less than 1.0E09 Ohms.
Chemical coatings that increase the conductivity of standard flooring may
provide a viable, cost effective alternative to installing new ESD flooring.
Thus, it is the goal of this study to provide documented evidence of coating
conductivity and to identify materials that meet the resistance levels for
reliable compliance. This
report documents a series of electrical conductivity test performed on
concrete filled testing trays rendered esd (static control) compliant
via the application of ElectraGlaze ESD Floor Finish, ElectraGuard ESD epoxy
Paint and ElectraSeal static control concrete sealer. Grounding of the
specimens comprised of an appropriately placed Copper 3' x 3' x .125 thick
panel reliably attached to primary electrical building ground and placed
beneath the concrete filled galvanized testing tray. The
following testing was performed in a temperature and humidity set to
replicate many typical job site environments.
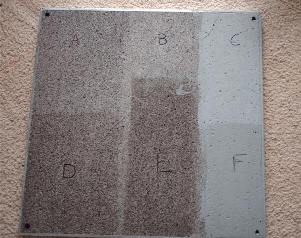
Click for Close Up of this
sample
Click for
better display of gloss characteristics
A)
ElectraSeal ESD
Concrete Sealers
B) Untreated
Concrete Filled Raised Access Panel.
C)
ElectraGuard ESD
Epoxy Floor Paint.
D) ElectraSeal top
coated with 2 coats of
ElectraGlaze ESD Floor
Finish.
E) Bare Concrete
coated with 2 coats of ElectraGlaze ESD Floor
Finish.
F) ElectraGuard ESD
Epoxy, top coated with 2 coats of ElectraGlaze.
Note: Testing
completed 6 days after application of coating systems. Ambient
environmental conditions: 28.6%rH @ 71.5 Deg F.
Material |
PTP
Resistance |
RTG Resistance |
Combination Resistance
(97.1) |
Pass/Fail |
A)
ElectraSeal Sealer |
6.41E07 |
2.63E07 |
9.38E07 |
PASS |
B)
Uncoated Tech Concrete (1) |
9.71E08 |
9.27E08 |
>1.0E09 |
FAIL |
C)
ElectraGuard** (2) |
2.81E04 |
1.64E04 |
1.02E06 |
PASS |
D)
ElectraSeal **/ ElectraGlaze** |
6.35E08 |
3.70E08 |
2.13E08 |
PASS |
E)
ElectraGlaze ESD Wax ** |
9.53E08 |
8.66E08 |
>1.0E09 |
FAIL |
F)
ElectraGuard** / ElectraGlaze** (2) |
7.94E05 |
6.04E05 |
1.26E06 |
PASS |
(**) 2 coats
(1) erratic
fluctuating readings, humidity dependent.
(2) Meets UL
standards for minimum resistance
Contact UNITED Static Control Products Inc
©
All rights Reserved
Published
12/09/2019
w3c compliant
* |