|
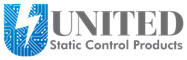
Note:
Titanium ESD vinyl flooring is resistant to most industrial
chemicals. Test methods, chemical concentrations, dwell time and
some environmental factors may cause a variation from the following
results. Pre-test on site prior to proceeding with the installation.
Chemical Resistance: Exposure
time, 30 minutes, top surface only
Sulfuric Acid (25%),
no effect |
Gasoline, Mineral
Oil, Vegetable Oil, no effect |
Sulfuric Acid (5%),
no effect |
Chloroform, no
effect |
Nitric Acid (Conc.),
Slight Surface Attack |
Trichloroethylene,
no effect |
Nitric Acid (5%), no
effect |
Acetone,
some
softening, no color change |
Hydrochloric Acid
(5%), slight dulling |
Methyl Ethyl Ketone,
slight surface dulling |
Acetic Acid (Conc.),
no effect |
Amyl Acetate, Ethyl Acetate, no
effect |
Acetic Acid (5%), no
effect |
Silver Nitrate
(40%), slight brown stain |
Sodium Hydroxide
(50%), no effect |
Ethyl Ether, no
effect |
Ammonium Hydroxide
(28%), no effect |
Formaldehyde (40%),
no effect |
Methyl Alcohol, no
effect |
Iodine, Yellow Stain |
Ethyl Alcohol, no
effect |
Phenol, slight
surface attack |
Cresol, slight
surface attack |
Benzene, no effect |
Xylene, no effect |
Carbon
Tetrachloride, no effect |
30%
hydrogen peroxide, No visible change* |
10:1 HF
dip (~5% HF), no visible change* |
Developer
321 (contains TMAH), no effect* |
Butyl Alcohol, no
effect |
Prestone
50/50 antifreeze/coolant, no effect |
Prestone DOT
3 brake fluid, no effect |
*client
testing
Chemical Resistance, 45 minutes under watch
glass
Antifreeze - No Effect |
Benzyl Alcohol - No
Effect |
Dodecylbenzene Sulfonic
Acid - No Effect |
Formic acid - No Effect |
Isopropanol (IPA) -
Slight Softening, No Color Change |
Mineral Spirits - No
Effect |
Napthol Spirits - No
Effect |
Octyl Alcohol - No
Effect |
Oxalic Acid - Slight
Dulling |
Phosphoric Acid
Technical Grade 75% - Very Slight Softening |
Sodium Hypochlorite 15%
(Bleach) - Slight Dulling |
Stearic Acid - No
Effect |
Sulfuric Acid 90% - No
Effect |
Tetrahydrofurfuryl
Alcohol - No Effect |
|
Brake Fluid - No effect |
Chemical Resistance of Interlocking Tiles
2 hour exposure to back and top of tile:
Silane Type 174
(Gamma-Methacryloxypropyltrimethoxysilane)
Results: Deforms tiles
Short Form
Performance Specifications
Surface Resistivity Point to
Point (ESD S 7.1) |
<1.0E09 |
Electrical Resistance to Ground
(ESD S 7.1) |
<1.0E09 |
Flooring Radiant Panel ASTM
E648; NBSIR 75-950: NFPA 254, Critical Radiant
Flux |
0.73 W/cm2, Class 1 |
Smoke Density, ASTM E-662; NFPA
258; Average optical density in burning /
smoldering mode |
<450 |
Residual Indentation LF-475A |
0.002 average |
Abrasive Wear, Taber H-18 wheel,
5,000 cycles, 1,000 gm weight |
1.1% loss of weight |
Abrasive Wear, Taber H-18 wheel,
1,000 gm weight to wear layer penetration (end
point) |
>20,000 cycles, (2.0% loss of weight |
Static coefficient of friction,
ASTM D-2047-03, James Test average wet, dry
leather |
.60 approx. |
Static load limit DIN 16961.2 |
>1,000 PSI |
Charge decay time per FTMS
4046-101c |
< 0.2 seconds |
ElectraFloor Titanium Series meets or exceeds the
requirements of Federal Specifications LF-475a and
SST-312b for flexibility, dimensional stability,
resistance to reagents and residual indentation.
Titanium Meets ANSI/ESD S20.20-2021
page 6, table 2 Product Qualification and Compliance
Verification
Roll goods may be used as mats or flooring. Titanium
Series ESD Flooring is manufactured in the European
Union for United SCP Incorporated, PO Box 19252,
Colorado City CO 81019. The material is manufactured as a co-extruded
4' 6" x 66' x .080 gauge
sheets a
24" x 24" x .080 gauge tile
or
3 mm thick Interlocking tile . Titanium series flooring
features a hard wear
resistant semi gloss ESD conductive top layer and a flexible full
surface conductive ESD backing for ultimate
electrical consistency and premier static control
performance.
CONTACT UNITED STATIC CONTROL PRODUCTS
*
|
|